AOMAG(ISO9001:2008 Certified) have been producing alnico magnets from 1996 in China. Alnico magnets (including Cast alnico Magnets - Sintered alnico Magnets), are made up of a composite of aluminum, nickel and cobalt with small amounts of other elements, have good temperature stability, good resistance to demagnetization, high residual induction, and relatively high energies. By strength, they are much weaker than Neodymium magnets, SmCo magnets and Ferrite magnets.
Alnico magnets, which can be customized, are produced by two typical methods, casting or sintering. Casting delivers higher energy products and allows for the design of intricate shapes. Sintering is usually restricted to smaller sizes and offers slightly lower magnetic properties, but has tighter dimensional tolerances due to its processing. Alnico magnets can be produced with either isotropic or anisotropic properties. Alnico 5 and Alnico 8 are anisotropic and exhibit a preferred direction of orientation, Magnetic orientation should be specified on your drawing when you send an order to us. Cast Alnico 5 is the most commonly used of all the cast Alnico's. It combines high indications with a high energy product of 5 MGOe or more and is used extensively in rotation machinery, communications, meters and instruments, sensing devices and holding applications.
![]() |
![]() |
![]() |
![]() |
![]() |
![]() |
Application
Alnico magnets have wide range of working temperatures, up to 550 degree Celsius. They have experienced renewed interest in recent years in such temperature-sensitive applications as hall-effect and MR-based automotive and electronic sensors, in addition to the traditional magnetron, TWT amplifiers, actuators, motors and instruments applications that have long relied upon alnico. Mainly used for a variety of Separators, Sensors, Electron tubes, Traveling wave tubes, Radar, Holding magnets, Clutches and bearings, Motors, Relays, Controls, Generators, Receivers, Telephones, Microphones, Bell ringers, Loudspeakers, Cow magnets, Educational products, military technology and other fields.
Alnico Magnets Material Overview
Excellent Temperature Stability
Alnico magnets were invented in the 1920s. Composed of aluminum, nickel and cobalt alloys, alnico magnets are used today in high temperature applications, in applications requiring low coercivities (the ability to demagnetize and re-magnetize easily), or in mass produced instruments and legacy applications where the material has been designed.On a cost per pound basis, this material is comparable to the cost of neodymium magnets. However, in most applications, alnico is much less powerful than Neodymium magnets. Alnico magnets are manufactured through either casting or sintering. Cast magnets can be made in fairly complex shapes such as a 4-pole round horseshoe magnet (see image below).
AOMAG Magnetics designs and builds custom alnico magnets and technical magnetic assemblies, manufactured to meet your specialty requirements. Send us a request for quote today for more information about standard & custom alnico magnets. Large inventory of alnico magnets are also available for on-line purchase at AOMAG .
Key Benefits of Alnico Magnet Material
- Excellent temperature stability up to 1,000° F; 90% of room temperature magnetization is retained up to this temperature.
- High residual induction: alnico magnets can produce powerful fields in certain configurations.
- Alnico material does not corrode.
- Cast alnico magnets can be produced in relatively complex shapes.
- Tooling for cast magnets is relatively low, since sand molds are generally used for the casting process.
Key Challenges of Alnico Magnet Material
- Alnico materials have low coercivities, so they are easily demagnetized.
- They are relatively costly, as they contain both nickel and cobalt.
- Cast alnicos often have casting pores and voids within them, which can be problematic from an aesthetic point of view, and because large voids may lower expected magnetic flux.
Quick Facts about Alnico Magnet Material
- Density: 0.265 lbs. per cubic inch
- Saturation magnetizing field required: about 5kOe
- Manufacturing methods: casting (most common), or sintering.
- Available Shapes: blocks, bars, discs, rings, horseshoes, etc.
- Available Grades: from about 0105 to 0519. (First 2 digits represent BHmax, and second two digits represent Intrinsic Coercivity, or Hci).
- Sizes: off tool, very large alnico magnets can be cast (horseshoe magnets weighing 500 lbs.); smaller magnets are usually sintered (sintered discs, 1/16" in diameter).
Special care should be taken to ensure that these magnets are not subject to adverse repelling fields, since these could partially de-magnetize the magnets. If alnicos are partially de-magnetized however, they can be easily re-magnetized.
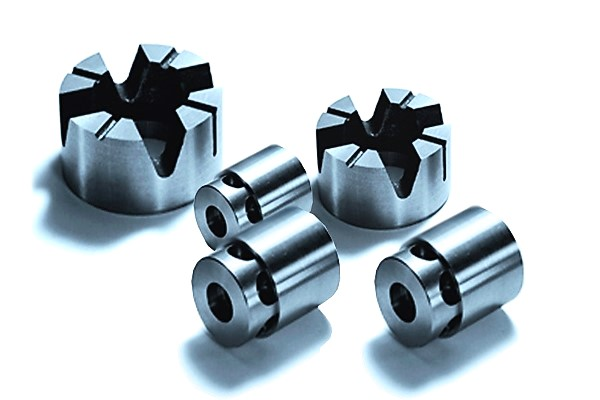
AOMAG Magnetics designs and builds custom alnico magnets, and magnetic assemblies, manufactured to meet your specialty requirements. Alnico magnets offer high magnetic remanence and have much lower coercivities than the ceramic and rare-earth types of magnet materials. Part of the permanent magnet family, alnicos are less brittle than rare-earth magnets and exhibit excellent temperature stability. They are manufactured through either a casting or sintering process and can be made into complex shapes, which are not possible
with some of the other magnet materials.
- Sizes & Shapes: Sizes range from small disc magnets, 1/16€ in diameter to large cast Alnico magnets weighing up to 500 lbs. Standard shapes include disc, rectangular, channel, horseshoe, rod, and rings in different dimensional specifications. Non-standard shapes can be custom fabricated to specifications from raw stock, and we can custom manufacture virtually any shape & size to meet your specialty requirements.
- Manufacturing: Alnico magnets are hard and brittle, and so are prone to chipping and cracking. Cast Alnico magnets may exhibit pores and voids common in cast materials. Machining or drilling cannot be accomplished by ordinary methods; cutting and grinding should be done prior to magnetizing. We are fully equipped to machine these materials to your specifications.
- Surface Treatments: Known for their excellent resistance to oxidation, alnico magnets do not typically require protective coating or plating.
- Temperature Considerations: Alnico magnets can be used at temperatures up to about 1,000°F (540°C), the highest temperatures at which any magnet material can be used. Approximately 90% of room temperature magnetization is retained up to 1,000°F (540°C).
- Magnetizing & Handling: Alnico magnets require magnetizing fields of only about 3-kilo Oersteds. Because of their low coercivities, special care should be taken to assure that these magnets are not subjected to adverse repelling fields which could partially demagnetize them. Alnico magnets should be stored with "keepers" which close the magnetic field in order to reduce the risk of demagnetization. However, if alnicos become partially demagnetized, they can be easily re-magnetized.
- Common Applications: Alnico magnets are commonly used in meters, instruments, sensing devices and very high-temperature applications.
- Material Information: For more information about this material and data sheets, visit the alnico magnet materials page